
®
Watch how the Alfaluz Workhorse solves the challenge of producing oil sands in the demanding conditions in Canada.
(5 minute video)
SOLVING OIL SANDS & TAILING POND CHALLENGES
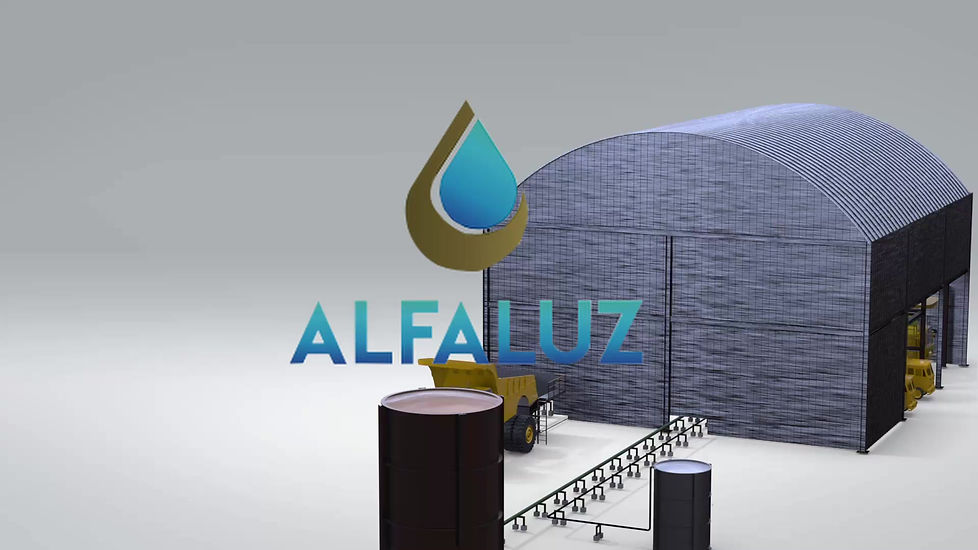
THERMAL (SAGD & OTHER) & MINING PRODUCTION CHALLENGES

Unconsolidated sandstone deposits known as oil sands are comprised primarily of sand, clay and water saturated with bitumen.
Bitumen is a highly viscous and extra-heavy hydrocarbon with an average API gravity of 8°. It can be separated into two organic compounds: asphaltenes and maltenes.
Asphaltenes have a heavy molecular structure, imparting a high viscosity and density to the oil. They contain nickel, sulfur, vanadium, and ultra-fine particles that reduce the quality of the produced crude oil and make it expensive and difficult to transport and refine.
The main challenge facing mining operations is obtaining higher profit margins from bitumen without generating toxic tailing ponds, for which the Workhorse is used. For thermal operations (SAGD and others), the challenge is to avoid requiring large amounts of diluent and chemicals, reduce greenhouse gas emissions, and reduce C02 emissions and energy costs. For these applications, the M-CRACK is used.
®
OUR M-CRACK SYSTEM IS THE ANSWER
Alfaluz’s cost-effective and 100% green M-CRACK system consists of a battery of specially designed equipment combined with Alfaluz's proprietary chemical Petromax®. quickly separates contaminants from heavy oil during the production process without the use of diluents, resulting in increased yield that is pipeline-ready.
The M-CRACK accomplishes this in three steps:



Step one instantaneously breaks the emulsion, eliminates H2S, and temporarily reduces the viscosity and density of heavy oil. By hydro-blasting the heavy oil with a mix of water and Petromax®, no diluents or heat is required.
Step two separates solids, sulfur, asphaltenes, crystalized paraffin, heavy metals and some salts, resulting in a lighter oil with lower viscosity, lower density, and fewer contaminants.
Step three separates the oil from water, resulting in two valuable outputs:
-
Pipeline-ready commercial oil.
-
Clean water which can be recirculated within the M-CRACK system, or used as processed water without the need for additional expensive treatments.

STEP 1: IT ALL STARTS WITH BREAKING THE EMULSION
The first step instantaneously breaks the emulsion by changing the bond between the inorganic particles and the hydrocarbons.
Once the electric charge changes to a negative state in the inorganic particles in the injection chamber, the particles and the hydrocarbons instantly repel each other, forming a pumpable slurry.
The pumpable slurry contains no H2S, solids free of oil, and oil free of solids, water, salt and heavy metals suspended in the water phase.
The M-CRACK injection unit hydroblasts Petromax® into the bitumen, instantaneously breaking the emulsion, with the following effects:
High-Pressure Penetration:
The resins that are covering the solids are penetrated by force and the strong bond with solids is broken (clay, sand, quartz, asphaltenes, others).
Mixing at High Pressure:
The solids are energized in order to create a flow in which the most complicated compounds will be suspended and uniformly dispersed (colloidal dispersion).
The shearing breaks the weaker bonds so Petromax® can encapsulate the solids such as the heavy molecular weight asphaltenes, some paraffin and heavy metals, so they will drop from the flow in the next step.

STEP 1 RESULTS: THE LESS DENSE, NON VISCOUS FLUID IS PRE-SEPARATED
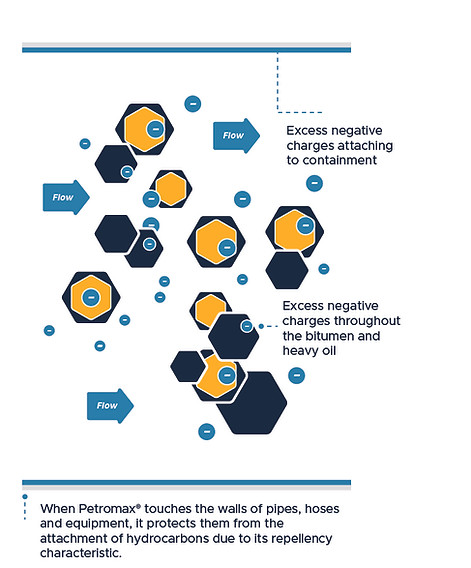
The injection chamber conditioning process produces an excess negative charge throughout the heavy oil that will be used in the next step.
At the end of this first step, we see a very homogeneous thick, dark, pumpable liquid.
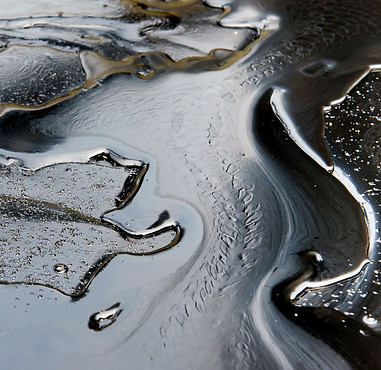
On average 50% of the asphaltenes are diluted and encapsulated by Petromax®, so they will be separated along with the sand and other fine and ultra-fine particles in the MCT separator unit during Step 2.
The slurry coming from the first step has the following improved characteristics:
-
The emulsion has been broken
-
The solids are free of hydrocarbons
-
Fine particles, some resins, some paraffin and black powder are suspended in the fluid (colloidal dispersion)
Step 2 of the M-CRACK system uses our proprietary hydro-cyclone MCT unit to separate fine particles, heavy metals, salts, asphaltenes, sulfur and black powder from the colloidal dispersion.
The MCT separater unit uses a number of advanced and proven forces to do it's magic.
​
What flows from Step 2 to Step 3 is a lighter, cleaner oil mixed with water.
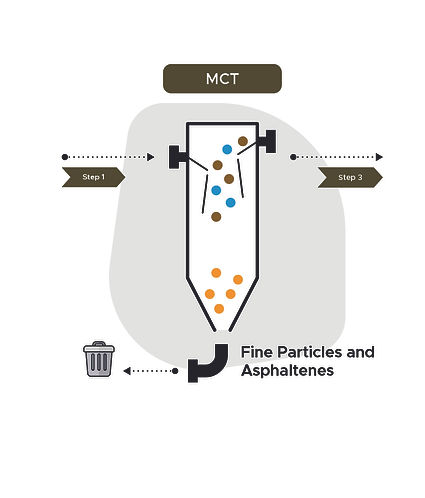
STEP 3: SEPARATE WATER FROM PIPELINE-READY OIL
The fluid coming from the MCT separator unit in Step 2 has permanently reduced density, viscosity, H2S and other contaminants.
​
It is a mix of cleaner and softer water with lighter oil (API gravity over 19).
During Step 3, the clean oil and water brought over from the MCT are separated using a highly efficient, off-the-shelf hydro-cyclone.
The result is two very valuable products that are created without using heat or diluents:
-
Pipeline-ready commercial oil.
-
Clean water ready to recirculate within the M-CRACK system, and/or use as processed water without the need for additional treatment.

STEP 2: ELIMINATE FINE PARTICLES & TOXIC MATERIALS
EXPLORE ADDITIONAL RESOURCES
